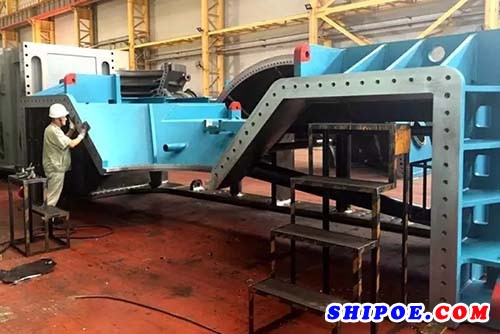
2016年,大連船柴承攬了6套哈汽低壓外缸的加工任務(wù),這個(gè)任務(wù)就交給了機(jī)械加工部。在加工過(guò)程中,制造部對(duì)外缸加工的工藝方法、工藝標(biāo)準(zhǔn)、轉(zhuǎn)序過(guò)程等,制定了詳細(xì)的作業(yè)流程和規(guī)范,堅(jiān)持對(duì)加工的每一道工序都進(jìn)行嚴(yán)格的監(jiān)督和檢驗(yàn)。在前3套外缸的報(bào)驗(yàn)過(guò)程中,發(fā)現(xiàn)雖然加工過(guò)程中外缸的尺寸公差都控制得很好,但在外缸電端和調(diào)端的垂直面結(jié)合處,有大約30mm*40mm面積部位合缸間隙值達(dá)不到圖紙要求,局部產(chǎn)生0.02mm的超差。
嚴(yán)謹(jǐn)?shù)臋C(jī)加人認(rèn)為,超差就是不合格。在后續(xù)加工過(guò)程中,他們對(duì)此問(wèn)題進(jìn)行了重點(diǎn)關(guān)注,并最終找出超差的原因:外缸結(jié)構(gòu)造成的變形所致。他們及時(shí)調(diào)整了工藝方法,在加工第四套107055外缸時(shí),把易超差部位的水平連接面加工為高度差為0.03mm的斜面。在11月2日的報(bào)驗(yàn)檢測(cè)中,測(cè)量間隙0.02mm,塞尺不入。至此,困擾機(jī)加人的外缸間隙超差問(wèn)題得到了圓滿解決。
在今后工作中,機(jī)械加工部將以“三個(gè)五”精細(xì)化質(zhì)量管理方法為指南,堅(jiān)持將“工藝規(guī)范化管理”作為工作重點(diǎn),抓好工藝實(shí)施過(guò)程的管理和控制,借鑒哈汽60萬(wàn)千瓦低壓外缸零缺陷通過(guò)報(bào)驗(yàn)的成功經(jīng)驗(yàn),確保 “過(guò)程輸出零缺陷”,為產(chǎn)品內(nèi)在質(zhì)量的提升、為公司建造精品主機(jī)貢獻(xiàn)堅(jiān)實(shí)力量。