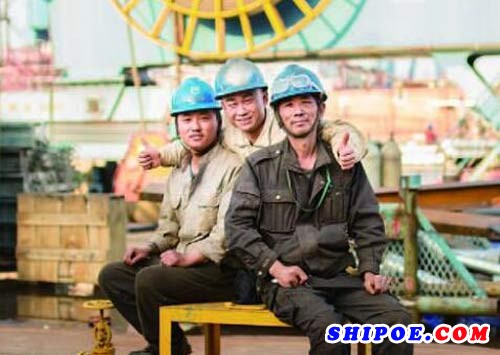
中航鼎衡造船有限公司(簡稱“中航鼎衡”),由中航國際控股,并由直屬企業(yè)中航國際船舶發(fā)展(中國)有限公司(簡稱“中航船舶”)受托管理。2017年是中航鼎衡持續(xù)抓管理基礎(chǔ)、優(yōu)化生產(chǎn)流程的關(guān)鍵一年,全體干部員工以“打造中小型化學(xué)品船建造示范基地”的工作目標(biāo)為指引,圍繞“提質(zhì)、增效、降本”三大年度工作主題,提質(zhì)增效工作取得了重要進(jìn)展。2017年初,船廠通過“SWOT”分析法,結(jié)合內(nèi)外部環(huán)境,明確了在安全、質(zhì)量、成本、研發(fā)和效率的“提質(zhì)增效”具體目標(biāo)。
安全生產(chǎn)促效益 科技興安顯人本
中航船舶、中航鼎衡將安全生產(chǎn)列為“必須做、立即做、嚴(yán)格做、限時做”且需要“革命性變化”的首要重點工作。船廠相繼借助集團(tuán)公司、總部特邀專家、外部船舶行業(yè)專家、第三方船級社、政府安監(jiān)部門、與中航威海間互查等多形式多次安全檢查,通過自查與交叉檢查的方式,解決自身可能產(chǎn)生的熟視無睹或長時間見怪不怪造成的隱患,安全隱患整改率100%,“零事故”有效保證了穩(wěn)定的生產(chǎn)環(huán)境,“以安全保效率,以安全促效益”。通過提高技術(shù)、運用智能化等手段營造“本質(zhì)安全”環(huán)境,船廠在“科技興安”方面下功夫,加大資金投入力度,相繼引進(jìn)登輪系統(tǒng)、機(jī)艙安全監(jiān)控系統(tǒng)、APP點檢巡查系統(tǒng)等管理軟件,借助高科技手段,提升安全監(jiān)控的及時性、有效性,初次嘗到了“高科技”改進(jìn)粗放式造船安全管理的甜頭。以人為本,進(jìn)一步改善了員工工作環(huán)境,努力打造“本質(zhì)安全”的施工作業(yè)環(huán)境。
推行“精益”質(zhì)量管理 穩(wěn)步提升產(chǎn)品品質(zhì)
船廠主打產(chǎn)品不銹鋼化學(xué)品船、雙燃料推進(jìn)動力船等均屬高難度、高標(biāo)準(zhǔn)、高附加值的產(chǎn)品,對分段建造、焊接質(zhì)量、合攏精度有著嚴(yán)苛的標(biāo)準(zhǔn)和要求。為此,船廠將“精益制造管理”作為提質(zhì)增效的著力點,一方面邀請中航國際商學(xué)院開展了“遠(yuǎn)航—展翅”培訓(xùn)計劃;另一方面,針對焊接、合攏成立工藝攻關(guān)小組,相繼推行無碼裝配、高效小車自動焊等工藝,加大精度控制管理力度,不斷提高中間產(chǎn)品的合格率。
成本攻堅 實現(xiàn)成本管控能力質(zhì)的提升
船廠開展成本專項管理提升,加強(qiáng)成本管控能力。一是成立成本管理中心,把好成本管控入口,從梳理人工定額、加強(qiáng)審價核減、預(yù)舾裝托盤定制及整理清理庫存積壓等多方面著手,促進(jìn)造船成本有效下降。
二是大力促進(jìn)采購費用降本工作,通過積極向船東推薦性價比更高的設(shè)備、引進(jìn)合適廠家創(chuàng)造有效競爭局面、減少中間環(huán)節(jié)等手段,在原材料價格大幅上漲的市場環(huán)境下,14艘新船項目的采購成本相較于報價預(yù)算,綜合降本率硬是達(dá)到了13.56%,深度挖掘降本空間。
三是多措施“節(jié)流”,降低費用支出,按月對費用執(zhí)行預(yù)算情況進(jìn)行分析統(tǒng)計及月度考核。
源頭入手 流程再造 推進(jìn)自主設(shè)計與生產(chǎn)的有效融合
2017年,船廠依托中航船舶、德他馬林(中國)及自身設(shè)計力量的有效融合,在16300噸雙燃料化學(xué)品船項目上開始試行自主生產(chǎn)設(shè)計工作,從設(shè)計源頭入手,優(yōu)化各類基礎(chǔ)資源配置、合理劃分分段建造規(guī)劃、及時溝通優(yōu)化現(xiàn)場問題,經(jīng)過首制船的驗證,僅貨艙區(qū)結(jié)構(gòu)優(yōu)化便減少了用鋼量61.6噸,初步達(dá)到了預(yù)期目標(biāo),實現(xiàn)了紙上造船的概念,為后續(xù)進(jìn)一步“降本增效”推進(jìn)分級、分道制造提供了翔實有力的基礎(chǔ)支持。
今年以來,中航船舶和船廠再次針對造船模式轉(zhuǎn)變工作進(jìn)行了深入研討,以“提質(zhì)增效”為導(dǎo)向,從碎片化、單點式向系統(tǒng)化全面推進(jìn)進(jìn)行轉(zhuǎn)變,從工位定置、中組建造、總組合攏、高效焊接等多個維度同步走。雖然其間由于經(jīng)驗不足,也產(chǎn)生了成本增加、效率降低的情況,但經(jīng)過近一年的堅定實施,從生產(chǎn)區(qū)域功能劃分、計劃管理體系、工序優(yōu)化組合、工藝工法等多方面多維度的優(yōu)化后,生產(chǎn)流程逐步固化,形成了符合船廠產(chǎn)品定位和資源特點的新流程體系,快速將“陣痛期”落下的工作量逐一完成,船舶建造效率尤其是船塢合攏效率得到了顯著提升,進(jìn)一步提高了核心資源的使用效率。在流程改進(jìn)后,分段總組率、預(yù)舾裝率分別從原有的50%、60%提升到現(xiàn)在的80%、85%,其中電氣舾裝件預(yù)裝率已達(dá)到95%,為縮短船塢合攏周期奠定了良好的基礎(chǔ),同時更為船廠爬坡蓄力、進(jìn)階“精益造船”模式奠定了堅實的基石。
建隊伍 抓機(jī)遇 努力打造船舶制造示范基地
建隊伍,夯實核心競爭力。持續(xù)優(yōu)化人力資源結(jié)構(gòu),建立合理的激勵、競爭機(jī)制,營造“能者上、庸者下”的用人氛圍,并積極借助中航國際商學(xué)院資源,開展課程培訓(xùn),以改變思維方式,打造目標(biāo)統(tǒng)一、行動統(tǒng)一、價值觀一致、知行合一的管理團(tuán)隊。 抓機(jī)遇,鞏固市場領(lǐng)先地位。隨著國際社會對“ECA”、“Tier III”等環(huán)保節(jié)能要求的日益增高,充分發(fā)揮自身在節(jié)能型船舶、雙燃料動力船舶方面積累的經(jīng)驗,謀求更多的合作機(jī)會。同時,堅持差異化市場定位,充分利用“軍民融合”中的市場融合,承繼航空工業(yè)、中航國際幾十余年積累的市場優(yōu)勢,利用自身的“全球第一”品牌效應(yīng),發(fā)揮我們天生基因中的航空探索精神,在中小型化學(xué)品船、液化氣船等細(xì)分領(lǐng)域抓機(jī)遇、謀發(fā)展,爭取更寬廣的市場前景。促融合,努力打造示范基地。通過與中航船舶、德他馬林的有效融合,踐行“互聯(lián)網(wǎng)+協(xié)同制造”,通過工業(yè)化與信息化的深度融合,及時收集并分析基礎(chǔ)管理數(shù)據(jù),探索“精益造船”的管理提升要求,夯實“精益制造”基礎(chǔ),向構(gòu)建“智能制造”穩(wěn)步前行,努力朝著打造“國內(nèi)領(lǐng)先,國際一流”船舶制造示范基地砥礪奮進(jìn)。